IGP-DURA®sky 9503E-A3
Matte effect powder coating in ultra-high weather-resistant quality with very good anti-graffiti properties.
download PDFCharacteristics
- Matte
- Smooth flow
- Pearl mica
- Ultra super durable facade quality,
10 years Florida
Material approvals
- Qualicoat Nr. P-1967, LIGHT, class 3
- Qualicoat Nr. P-1968, MEDIUM, class 3
- Qualicoat Nr. P-1969, DARK, class 3
- AAMA 2605-20, independent test report
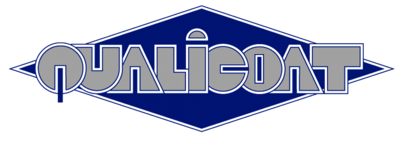
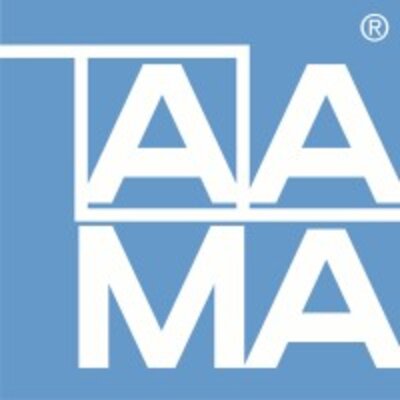
Powder properties
Film properties
ASTM D2247, Blister Size No. 8
Figure No.4
Processing
The substrate must be free from oil, grease and oxidation products. The pretreatment depends on the type of substrate and the corrosion protection to be achieved. We recommend the following pretreatments:
- Chromating according to DIN EN 12487
- Pre-anodization
- Chrome-free pretreatment according to GSB International and QUALICOAT specifications
- Zinc phosphating
- Zinc phosphating
- Chrome (III) passivation
- Chromating according to DIN EN 12487
For white and light IGP-DURA®sky qualities, the use of IGP-KORROPRIMER 6007A90164A01 is recommended as a primer.
For improved corrosion protection for applications on steel / galvanised steel, the use of corrosion protection primer IGP-KORROPRIMER 60 is recommended.
The suitability of the pretreatment method used is generally to be tested by the coater in advance with appropriate test methods. The minimum requirement for aluminium substrates / galvanised steel components is to carry out a boiling water test with a subsequent cross-cut adhesion and tape test. We refer to the guidelines of the GSB International, Qualicoat and Qualisteelcoat certifications. For further information: see also our special leaflet on pre-treatment (IGP-TI 100).
For the construction and operation of powder coating plants, the following regulations must be complied with: ATEX RL 2014/34/EU, EN 50177, DIN EN 16985.
For a pre-calculation of the required powder coating quantity, the necessary coating thickness must be determined for each article.
TObject | t min | t max |
---|---|---|
200 °C | 15 minutes | 20 minutes |
210 °C | 12 minutes | 17 minutes |
Due to e-caprolactam emissions during the curing process it is necessary to take care for a good ventilation to comply with the permitted occupational exposure limits concentrations.
Further information
- The contact time of the gaffiti with the surface must be kept as brief as possible
- Preliminary tests to select a suitable graffiti remover
- Thorough rinsing of the cleaned areas with water
- The contact time of the graffiti remover with the surface must be kept as brief as possible
IGP recommendation:
- Elite 007 grafitti remover from Crous Chemicals GmbH
- Socostrip T4210P from Socomore
- Bonderite S-ST 1302 and Bonderite C-MC 400 from Henkel AG
- or a different non-abrasive cleaner